The Scientific Research Behind Porosity: A Comprehensive Guide for Welders and Fabricators
Comprehending the detailed devices behind porosity in welding is important for welders and fabricators making every effort for remarkable workmanship. From the composition of the base products to the ins and outs of the welding procedure itself, a wide range of variables conspire to either aggravate or alleviate the presence of porosity.
Comprehending Porosity in Welding
FIRST SENTENCE:
Evaluation of porosity in welding exposes important understandings right into the integrity and top quality of the weld joint. Porosity, characterized by the existence of dental caries or voids within the weld steel, is a typical worry in welding processes. These gaps, otherwise appropriately resolved, can compromise the architectural stability and mechanical buildings of the weld, resulting in potential failings in the completed item.
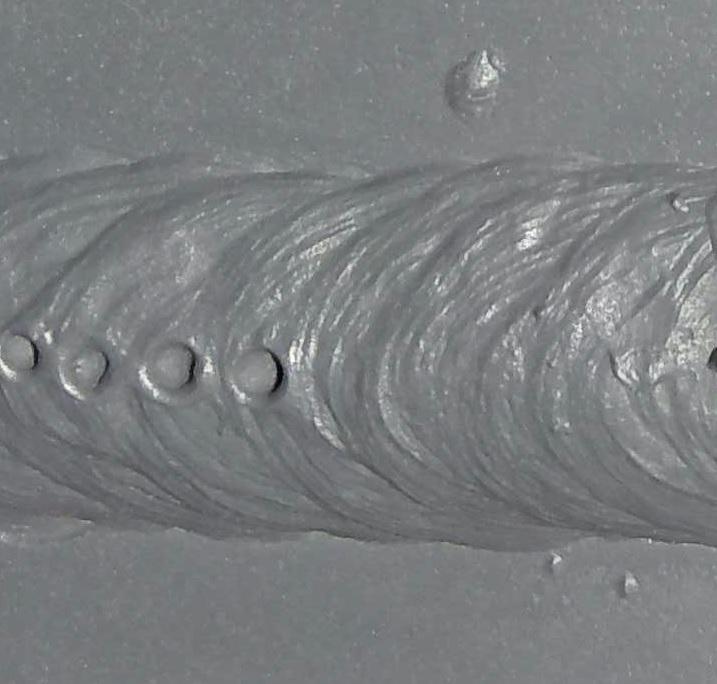
To find and evaluate porosity, non-destructive testing methods such as ultrasonic screening or X-ray examination are commonly utilized. These strategies allow for the identification of inner issues without endangering the integrity of the weld. By evaluating the size, form, and circulation of porosity within a weld, welders can make enlightened choices to enhance their welding processes and achieve sounder weld joints.
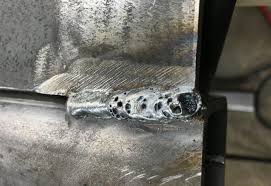
Variables Affecting Porosity Formation
The occurrence of porosity in welding is affected by a myriad of elements, ranging from gas securing efficiency to the ins and outs of welding specification settings. One essential factor contributing to porosity development is inadequate gas securing. When the securing gas, typically argon or carbon dioxide, is not successfully covering the weld pool, climatic gases like oxygen and nitrogen can pollute the molten metal, resulting in porosity. Additionally, the sanitation of the base materials plays a substantial function. Pollutants such as rust, oil, or wetness can evaporate throughout welding, producing gas pockets within the weld. Welding specifications, including voltage, existing, take a trip speed, and electrode type, also effect porosity development. Using improper settings can produce excessive spatter or warm input, which in turn can lead to porosity. The welding technique used, such as gas metal arc welding (GMAW) or secured metal arc welding (SMAW), can affect porosity formation due to variations in warmth distribution and gas insurance coverage. Comprehending and regulating these variables are vital for decreasing porosity in welding operations.
Results of Porosity on Weld Top Quality
The visibility of porosity likewise compromises the weld's resistance to rust, as the caught air or gases within the spaces can react with the surrounding setting, leading to deterioration over time. Furthermore, porosity can hinder the weld's capability to withstand pressure or effect, more threatening the general top quality and reliability of the welded framework. In crucial applications such as aerospace, auto, or structural buildings, where security and longevity are extremely important, the damaging effects of porosity on weld top quality can have severe consequences, highlighting the significance of decreasing porosity through correct welding techniques and procedures.
Techniques to Lessen Porosity
In addition, utilizing the proper welding criteria, such as the right voltage, current, and take a trip speed, is important in preventing porosity. Preserving a regular arc size and angle during welding also aids lower the likelihood of porosity.

Making use of the appropriate welding technique, such as back-stepping or using a weaving motion, can additionally assist distribute warmth evenly and minimize the opportunities of porosity development. By applying these techniques, welders can successfully lessen porosity and produce top quality bonded joints.
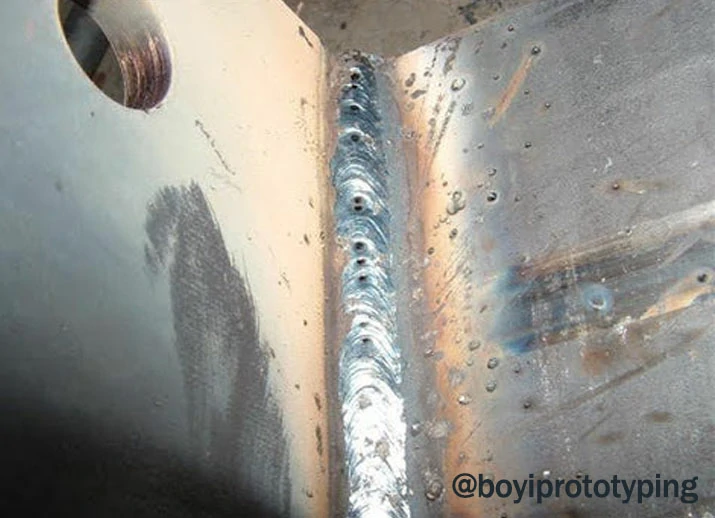
Advanced Solutions for Porosity Control
Applying sophisticated innovations and ingenious approaches plays click here to find out more an essential role in attaining superior control over porosity in welding processes. One sophisticated service is making use of advanced gas mixtures. Securing gases like helium or a mixture of argon and hydrogen can help in reducing porosity by giving far better arc security and improved gas protection. Additionally, utilizing advanced welding methods such as pulsed MIG welding or modified environment welding can also assist minimize porosity issues.
Another innovative remedy includes using sophisticated welding tools. Making use of tools with integrated functions like waveform control and sophisticated power resources can boost weld quality and decrease porosity risks. The implementation of automated welding systems with exact control over parameters can dramatically reduce porosity defects.
Moreover, integrating innovative monitoring and assessment modern technologies such as real-time X-ray this content imaging or automated ultrasonic screening can aid in spotting porosity early in the welding process, permitting immediate restorative activities. On the whole, integrating these innovative remedies can substantially enhance porosity control and enhance the general top quality of welded components.
Conclusion
In final thought, recognizing the informative post scientific research behind porosity in welding is important for welders and makers to create top quality welds. By recognizing the aspects influencing porosity development and executing techniques to minimize it, welders can improve the total weld high quality. Advanced services for porosity control can further boost the welding procedure and guarantee a solid and reputable weld. It is very important for welders to continually inform themselves on porosity and implement ideal methods to achieve optimum results.